Injection blow molding is a hollow plastic bottle produced by injection blow molding equipment, and injection stretch blow molding is a hollow plastic bottle produced by injection stretch blow molding equipment. These two molding processes and the extrusion blow molding process are currently the most important plastic hollow blow molding processes.

A brief introduction to the development history of injection blow molding and injection stretch blow molding
Compared with injection molding, extrusion, and other processing technologies, the blow molding process has developed relatively late.
Its process principle comes from the blowing process of glass bottles or glass products. In the 1930s, the first bottle blowing machine came out, but due to the limitations of equipment and materials, it did not develop rapidly at the beginning and was only used to produce low-density polyethylene bottles. In the 1950s, with the gradual development of high-density polyethylene and other new materials and the development of molding equipment, the blow molding process began to develop greatly, and bottles of different materials, structures, and sizes were gradually widely used in various industries. in the industry.
The real industrialization of the injection-blowing process began in the late 1960s. Në 1969, Zuma Corporation of the United States introduced the first commercial plastic injection and blowing equipment to the market. Through decades of development, many different types and functions of various types of injection and blowing equipment have been developed. The injection blowing process has become one of the most important molding processes in the bottle blowing industry.
The injection stretch blow molding process (ISBM), also known as the injection stretch blow molding process, was not industrialized until 1970. Since then, the application of various materials, mainly PET, has made it develop rapidly in recent decades. It is now widely used in the packaging of medicines, ushqimi, beverages, water, kozmetike, condiments, edible oils, and even various household items and alcohol.
The development of the blowing industry in my country only started in the 1980s. As various industries have entered a period of rapid development, there is a huge demand for various plastic bottles. In order to meet the needs of the market, my country has begun to continuously introduce foreign advanced bottle blowing production equipment, and gradually replace glass bottles with plastic bottles, laying the foundation for the industrialization of bottle blowing. Up to now, the market size of the blowing process has covered almost all daily necessities, fast-moving consumer goods, and pharmaceutical industries. Në të njëjtën kohë, a number of highly professional bottle-blowing manufacturers were born.
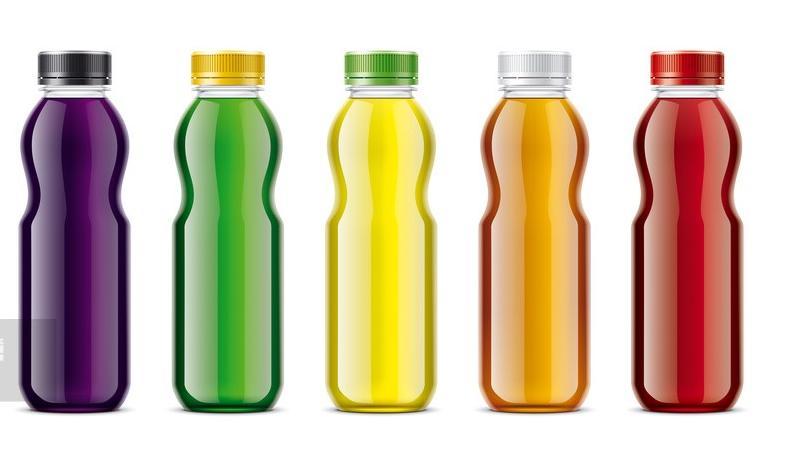
Introduction of secondary processing technology
Compared with traditional paper and film packaging, plastic bottle packaging not only has the advantages of better protection and convenience for multiple uses but also makes the product look more beautiful and high-end. In order to make the bottle more beautiful and have the function of transmitting and identifying commodity information, in addition to designing the appearance structure of the bottle itself, it is usually matched with certain secondary processing technology to give the bottle some colors, patterns, characters or special surface effects. The following is a brief introduction to the secondary processes commonly used in injection blowing and injection stretch blowing.
Mold and material design can process effects
The appearance and surface gloss of injection-blown and injection-stretched bottles are quite exquisite. For bottles that do not require a very high appearance, they can also have some simple aesthetic effects or text pattern information through bottle mold design and material formula design. Për shembull, through the mold design, the bottle can have the common smooth or frosted effect, concave or convex text, pattern or LOGO, etj. Through the material formula, the transparency and color of the bottle can be designed, including special metal, pearl, or phantom effects.
Selection and introduction of secondary processing technology
For bottle packaging with high appearance requirements, especially cosmetic packaging, a simple mold or material design cannot meet the requirements, and one or more secondary processing processes need to be added to increase aesthetics and transmit more information. The following is an introduction to some commonly used secondary processing techniques.
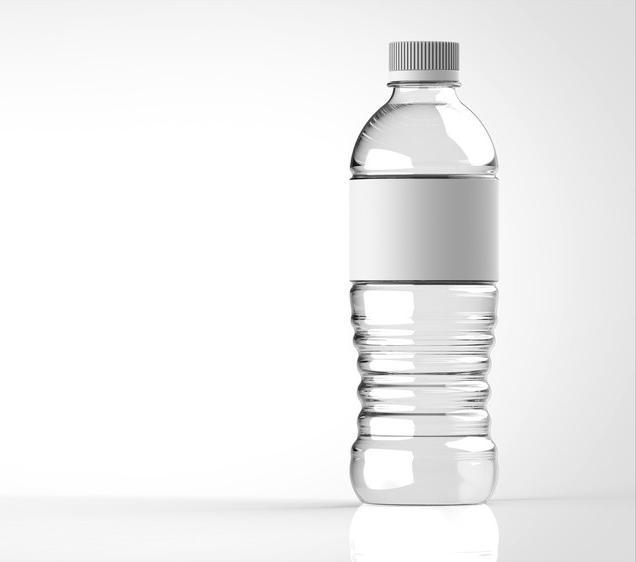
01 silkscreen
Screen printing is an important secondary processing method for bottles. Under the action of a squeegee, the ink carried on the screen plate that has been made according to the corresponding characters and patterns is printed on the surface of the bottle and then cured by UV lamp irradiation, so as to form the desired shape on the surface of the bottle. The processing technology of text patterns.
The silkscreen printing process has its very distinctive characteristics: because the pattern or text is directly printed on the surface of the bottle, it is integrated with the bottle, and the printed content has a bumpy touch, thus giving consumers a delicate and high-end feeling. Therefore, it is widely used in the packaging of cosmetics and daily chemical industries. But at the same time, there are some disadvantages that limit it to a certain extent. For the case where multiple colors need to be printed, because it must be printed color by color, the single-color equipment needs to be repeatedly printed many times, and the multi-color equipment also needs multiple stations to print and cure in sequence. The efficiency will be lower and the cost will be higher. On the other hand, due to the limitation of process characteristics, the fineness and overprinting accuracy of printed patterns and characters are low. Therefore, it is impossible to form large-area patterns with rich colors and delicate colors.
There are several key factors in the silk screen printing process of the bottle:
The first is the pretreatment of the bottle. The surface tension of the bottle is directly related to the problem of ink firmness after printing. Në përgjithësi, the surface tension of the material needs to reach 50 dyn/cm, and the ink firmness after printing is more guaranteed. Products with strong material polarity can be directly printed. Although PET material bottles are of weak polarity, with the selection of appropriate inks, PET bottles can basically be printed directly without surface treatment. For bottles of non-polar materials such as PP and PE, the surface of the bottle must be treated. The general treatment method is flame treatment or corona treatment. A simple way to judge is to observe whether the surface of the bottle on the dyne droplet can be spread out, that is, it can be “hanging on water” to indicate that the surface treatment effect meets the requirements.
The second is the quality of the screen printing screen. The wear resistance, mesh number, tension, and thickness of the photosensitive adhesive of the screen material have a great influence on the quality of the screen printing pattern, ink thickness, ink curing, and service life.
The third is the choice of ink. Different inks have different adhesion to the bottle surface of different materials, and different color inks have different energy requirements for curing. Therefore, to ensure the fastness of the ink, it is necessary to select the appropriate link for the substrate of the bottle. If you still can’t meet the requirements, you can try adding an appropriate amount of auxiliary solvents such as a curing agent to the ink.
Lastly is the UV light. UV lamps are the key equipment for ink curing. Different ink compositions, colors, and thicknesses require different energy for curing. With different printing areas, the selection of UV lamp specifications is also different. Therefore, the reasonable selection of UV lamps is also the key to fully ensuring the fastness of the ink. Whether the UV lamp meets the requirements can be assessed by testing the effect of the sample. After a certain period of use, it is also necessary to check and verify whether the UV lamp is aging. If it does not meet the requirements, it needs to be replaced with a new UV lamp.
02 labeling process
The second common secondary process for injection blow and injection stretch blow bottles is labeling. The labeling process is to apply the label to the surface of the bottle through various labeling equipment and processes. Commonly used label materials include plastic film and paper, which have a wide range of adaptability to the size and shape of the bottle and can be labeled on flat, curved, and cylindrical surfaces.
Compared with silk screen printing, the labeling process is simple, the cost is lower, and the appearance is exquisite. The label can be printed with more colors and the printing accuracy is higher, which can give the bottle richer and more exquisite patterns and more content information. Therefore, it is currently widely used in the pharmaceutical, ushqimi, and daily chemical industries.
With the development of the labeling process, the in-mold labeling process, which was widely used in injection molding and extrusion blowing, has also been gradually applied to injection blowing and injection stretch blowing. In-mold labeling has further advantages over ordinary labeling.
Së pari, in-mold labeling reduces production links, saves site space, and reduces labor costs. Përveç kësaj, the in-mold label is integrated with the bottle, and the bottle will appear more exquisite and high-end. Megjithatë, the in-mold label has certain requirements for the production mold. In addition to the need for the equipment mold to have an operating space, it is also necessary to design and electrostatically treat the mold exhaust, ndryshe, there will be poor labeling or label drop. Në të njëjtën kohë, since the in-mold labeling needs to adsorb the label on the inner wall of the bottle mold through static electricity or negative pressure, and the injection blowing and injection stretch blowing bottle molds are two-piece structures, the injection blowing and injection stretch blowing bottle in-mold labeling cannot be performed. Circumferential labeling is achieved. This can be achieved in ordinary labeling.
03 bronzimi
Hot stamping is also a relatively common post-processing method, which is often used in cosmetic bottle packaging. Gold or silver key patterns or words are formed on the surface of the bottle mainly through the bronzing process. Because of its prominent metal effect, it can enhance the decorative effect and grade of the bottle.
There are several points to pay attention to in the bronzing of the bottle: first, the rigidity and thickness uniformity of the bottle should be better; the second is to choose the appropriate anodized aluminum bronzing foil; the third is to use the bronzing plate with excellent quality; the last is the appropriate bronzing temperature and pressure.
04 spray
For cosmetic bottle packaging with higher appearance requirements, a color coating can also be sprayed on the inner or outer surface of the bottle. Colors can be uniform, gradient, or even multi-colored. In this way, the color effect and surface gloss that cannot be formed by the direct coloring of the material can be achieved, and the appearance and grade of the bottle can be improved.
